What is Sheet Metal Gauge?
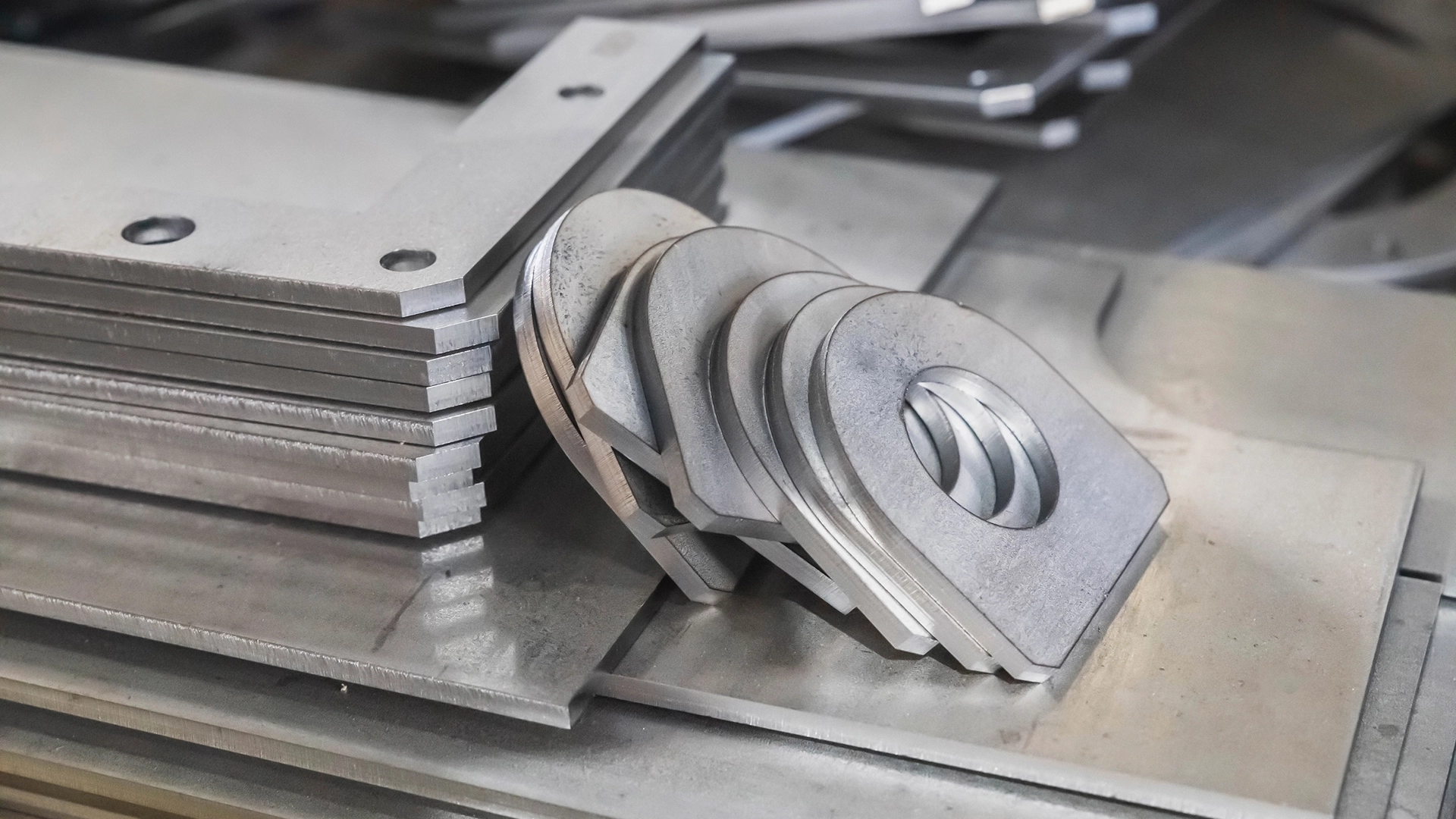
Understanding Sheet Metal Gauge Thickness
Sheet metal gauge thickness is crucial for anyone working with metal. It's all about knowing how thick or thin your sheet metal is. But here's the catch: the gauge system isn't tied to standard or metric measurements. Confusing, right?
The gauge system uses numbers to indicate thickness. The smaller the number, the thicker the metal. An 18-gauge steel sheet is thicker than a 20-gauge one. But these numbers don't tell you the exact thickness in inches or millimeters. That's where gauge charts come in handy.
Gauge charts convert these numbers into actual thickness. For example, 18-gauge steel is 0.0478 inches or 1.214 millimeters thick.
- Steel Example: 18-gauge steel is 0.0478 inches (1.214 mm)
- Aluminum Example: 18-gauge aluminum is 0.0403 inches (1.024 mm)
Why is this important? Knowing the exact thickness ensures your parts fit together perfectly. Whether you're bending, cutting, or assembling, the right gauge guarantees precision and reliability.
Next time you're working on a project, grab a gauge chart. It’s your best friend for getting those dimensions spot on.
Common Material Gauge Charts
Mild Steel | ||
---|---|---|
Gauge | Inches | MM |
7 | 0.1793 | 4.554 |
8 | 0.1644 | 4.175 |
9 | 0.1495 | 3.797 |
10 | 0.1345 | 3.416 |
11 | 0.1196 | 3.038 |
12 | 0.1046 | 2.656 |
14 | 0.0747 | 1.897 |
16 | 0.0598 | 1.518 |
18 | 0.0478 | 1.214 |
20 | 0.0359 | 0.911 |
22 | 0.0299 | 0.759 |
24 | 0.0239 | 0.607 |
26 | 0.0179 | 0.454 |
28 | 0.0149 | 0.378 |
Aluminum | ||
---|---|---|
Gauge | Inch | MM |
7 | 0.1443 | 3.665 |
8 | 0.1285 | 3.264 |
9 | 0.1144 | 2.906 |
10 | 0.1019 | 2.588 |
11 | 0.09074 | 2.305 |
12 | 0.08081 | 2.053 |
14 | 0.06408 | 1.628 |
16 | 0.05082 | 1.291 |
18 | 0.04030 | 1.024 |
20 | 0.03196 | 0.812 |
22 | 0.02535 | 0.644 |
24 | 0.0201 | 0.511 |
26 | 0.01594 | 0.405 |
28 | 0.01264 | 0.321 |
Stainless Steel | ||
---|---|---|
Gauge | Inch | MM |
7 | 0.1874 | 4.76 |
8 | 0.17187 | 4.365 |
9 | 0.15625 | 3.968 |
10 | 0.14062 | 3.571 |
11 | 0.125 | 3.175 |
12 | 0.10937 | 2.778 |
14 | 0.07812 | 1.984 |
16 | 0.0625 | 1.587 |
18 | 0.050 | 1.270 |
20 | 0.0375 | 0.9525 |
22 | 0.03125 | 0.7937 |
24 | 0.025 | 0.635 |
26 | 0.01875 | 0.476 |
28 | 0.01562 | 0.396 |
Factors to Consider When Choosing Gauge Thickness
Choosing the right sheet metal gauge thickness isn't just about picking a number off a chart. It's about understanding the specific needs of your project. Here are some key factors to consider:
- Strength Requirements: Think about the load your project will bear. Thicker gauges offer more strength. For example, if you're building a support structure, opting for a thicker gauge ensures durability. Choosing the wrong thickness can lead to structural failures.
- Weight Considerations: Weight is crucial, especially for projects where mobility is a factor. Lighter gauges might be sufficient for non-load-bearing parts, like decorative elements. But if weight isn't an issue, thicker sheets can provide added robustness.
- Corrosion Resistance: Certain metals offer better corrosion resistance at specific thicknesses. For outdoor projects or those exposed to harsh environments, selecting a gauge that complements the metal's natural resistance can extend the lifespan of your project. To make an informed decision, you might want to explore more about selecting the best metals for laser cutting, which details the strengths and weaknesses of various metals.
- Cost Implications: Thicker sheets generally cost more. Balancing between material costs and project requirements is essential. Sometimes, a slight reduction in thickness can save significant costs without compromising functionality.
Considering these factors helps ensure your project is both cost-effective and fit for purpose. Each decision impacts the final outcome, so weigh these considerations carefully.
Material Availability and Design Considerations
Material availability is a big deal when designing sheet metal parts. Before diving into your design, chat with your manufacturer about what gauges they have in stock. This can save you from headaches later.
Designing for thicknesses they don’t have? That can lead to costly adjustments and delays. No one wants that. It's best to stick to what's readily available.
Working with a manufacturer that stocks a wide range of gauges and prioritizes rapid delivery can streamline everything. When you know what’s available, you can design more efficiently.
- Stock Availability: Always ask what gauges are in stock. Designing with available materials avoids unnecessary delays.
- Proactive Communication: Discuss your needs with your manufacturer upfront. This can prevent costly changes down the line.
- Cost Efficiency: Using available materials can save you money. Custom orders or special thicknesses can drive up costs.
- Design Flexibility: Knowing what's in stock allows you to tweak your design for better results without compromising on quality.
For example, say you’re planning to use a specific gauge that’s not in stock. If you consult with us early, we might suggest a similar gauge that’s readily available, saving time and cost.
By keeping these considerations in mind and maintaining open communication, you can avoid common pitfalls and ensure a smoother design and production process. For more detailed guidelines on bending sheet metal and ensuring your designs meet all necessary specifications, check out our bending guidelines and tolerance specifications.
Additionally, for insights on optimizing your sheet metal manufacturing process and efficient ordering, visit our blog for valuable tips and guides.
Key Takeaways on Choosing Sheet Metal Gauge Thickness
Understanding sheet metal gauge thickness is key for any project. It’s not just about picking a number. You need to consider several factors to make sure your parts fit and perform as expected.
- Gauge System: Smaller numbers mean thicker metal. But gauges vary by material. Always check a gauge chart to know the exact thickness.
- Project Needs: Think about strength, weight, and corrosion resistance. Thicker gauges offer more strength but can add weight. For outdoor projects, choose a gauge that complements the metal’s natural resistance.
- Cost vs. Benefit: Thicker sheets often cost more. Balance material costs with your project requirements. Sometimes, a slight reduction in thickness can save money without compromising quality.
- Material Availability: Always check what your manufacturer has in stock. Designing for unavailable gauges can cause delays and extra costs. Open communication with your manufacturer can help streamline your project.
Choosing the right gauge thickness is about making informed decisions. Consider strength, weight, corrosion resistance, cost, and availability. Consult with your manufacturer to ensure you’re using the best material for your needs.
By keeping these points in mind, you’ll ensure your project is both efficient and effective.
Fast Track Your Project .
Seamless process, unparalleled precision, unbeatable speed. Turn your design into reality by beginning your journey with us today.
or drag and drop
.STEP / .STP up to 25MB
Your file are safe, secure and retain all intellectual rights.