Tapping vs PEM
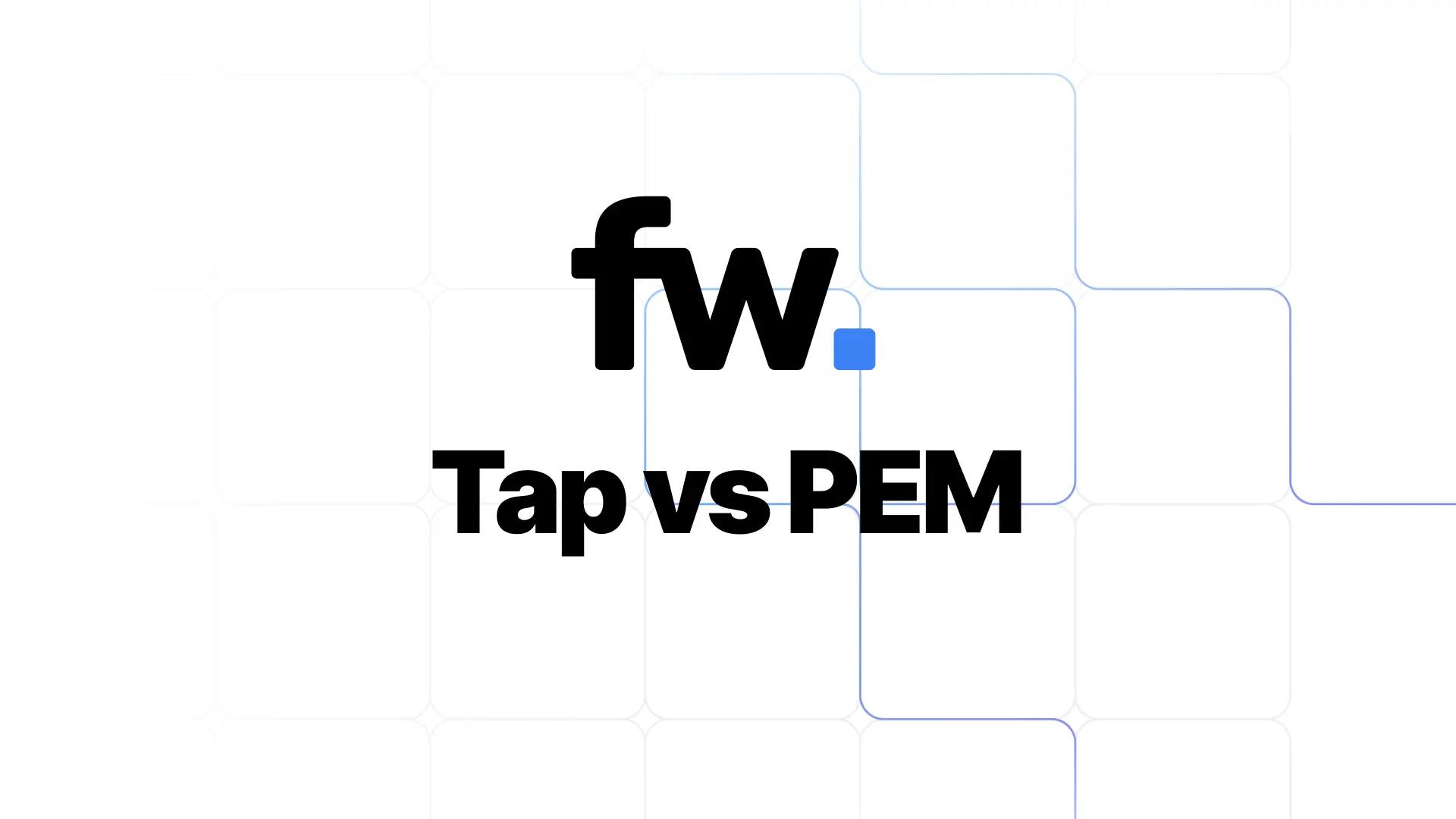
When it comes to tapping versus using PEM hardware, the choice largely depends on your specific application needs, including mechanical requirements and ease of assembly. Here’s a guide to help you understand the differences and make an informed decision
What is Tapping
Tapping involves creating internal threads in a pre-drilled hole to accept a screw or bolt. It’s a mechanical process where a tap tool is used to cut threads into a material.
Advantages of Tapping
- Strong Mechanical Hold: Tapped threads provide a strong mechanical connection, which is beneficial for applications requiring robust fastening.
- Versatility: Can be used in a variety of materials, including metals, plastics, and composites.
- Cost-Effective: Tapping is generally less expensive than other methods, especially for small production runs.
Disadvantages of Tapping
- Labor-Intensive: Requires precise drilling and tapping, which can be labor-intensive and time-consuming.
- Material Limitations: The tapped threads can weaken the material, especially in softer or thinner materials.
- Thread Wear: Threads can wear out or strip over time, especially under repeated assembly and disassembly.
Applications
- Commonly used in metalworking and assembly of parts where strong mechanical connections are needed.
- Ideal for applications where frequent disassembly and reassembly are required.
- Parts with thick enough material to make tapping feasible.
What is PEM Hardware
PEM hardware refers to a range of fasteners that are pressed into place without the need for threads. These are often used for quick assembly, and when your material is not thick enough for strong threads.
Advantages of PEM Hardware
- Quick Assembly: PEM hardware is designed for fast insertion and assembly, reducing production time.
- Reduced Material Stress: Typically less stress on the material compared to tapping, which can be beneficial for thinner or more delicate materials.
Disadvantages of PEM Hardware
- Initial Cost: The cost of PEM hardware can be higher than tapping, especially for small quantities or custom designs.
- Special Equipment: May require specific insertion tools or machinery, adding to setup costs.
- Less Versatile: Primarily suited for specific applications and materials, like PCBs or thin sheet metals, and not always adaptable to all designs.
Applications:
- Used to reduce part count by integrating the fastener with the part itself.
- Saves weight over thickening material for the purpose of tapping.
- Used in automotive, aerospace, and consumer electronics where quick assembly and reliability are paramount.
Choosing Between Tapping and PEM Hardware
- Material Considerations: Assess the material you’re working with. Tapping is versatile but may weaken certain thinner materials. PEM hardware is gentle on materials but may not be suitable for all types.
- Production Volume: Consider the scale of your production. Tapping might be cost-effective for smaller runs, whereas PEM hardware could be more efficient for larger volumes despite higher initial costs.
- Assembly Process: Evaluate the ease and speed of assembly. PEM hardware often provides faster assembly and can reduce labor costs, which is important for high-volume production.
- Durability and Maintenance: Think about how often the parts will be assembled and disassembled. Tapped threads can wear out over time especially in softer materials, while PEM hardware is designed for durability in repeated use.
Summary
Choosing between tapping and PEM hardware depends on material, volume, and assembly needs. Tapping is strong and versatile but labor-intensive and can weaken thin materials. PEM hardware enables fast, low-stress assembly, ideal for high volumes but involves higher initial costs and specialized equipment. Tapping suits smaller runs and varied materials, while PEM is efficient for large-scale production.
Designing around PEM hardware
For more information about how to integrate PEM hardware into your designs check out our Guide on Designing with PEM Hardware
What is Sheet Metal Gauge?
Navigate the complexities of choosing sheet metal gauge thickness with ease. Learn key factors for project success and avoid costly mistakes.
Understanding Yield Strength vs Tensile Strength
Explore the key differences between yield strength and tensile strength with our concise guide.
Fast Track Your Project .
Seamless process, unparalleled precision, unbeatable speed. Turn your design into reality by beginning your journey with us today.
or drag and drop
.STEP / .STP up to 25MB
Your file are safe, secure and retain all intellectual rights.